Knowing the tasks that need to be completed each day brings order and efficiency to your brewery. Having a production plan lets you and your staff know what is coming up for the days/weeks/months ahead. While a production plan is valuable, how do you effectively create one? This is a task that is perfectly suited to optimisation.
Optimisation and production planning
Getting straight to the point, how does optimisation and production planning fit together? First, we need to think about the challenge that we are trying to overcome: given a list of beers that need to be brewed, how do we determine which days and what equipment is needed to brew all beers.
Depending on your setup and how you brew, this could be really simple. For example, if you only brew ales that require 7 days fermentation time, then if you have 5 fermentation vessels you can simply brew a new beer every day. However, if you brew a range of different beer types, like most craft breweries, and have a large number of fermentation vessels, then the challenge of determining a effective production plan becomes much bigger.
We discussed the concept of optimisation and how it could help your brewery in a previous blog post. Production planning is just an application of optimisation. It could possibly be the most critical part of the brewery where optimisation can be a massive benefit. The following will detail an example on how optimisation can be used for production planning.
The beers

We start this example with the most important component, the beers. For this brewery we have 4 beer types that are being brewed: IPA, Pale Ale, Pilsner and Lager. They have different fermentation times. Also, the Pilsner and Lager both require conditioning time. The different fermentation and conditioning times introduces challenges in generating a production plan by hand. Note that the fermentation and conditioning times are just artificial to make the example a little more interesting from the scheduling point of view.
The equipment
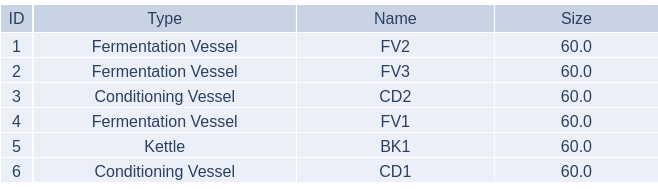
The brewery is quite a small brewery, but it has the main components to demonstrate the use of optimisation. In this example, we have one brew kit, five fermentation vessels and a single conditioning vessel. I have put a size on the fermentation and conditioning vessels of 60 hectolitres. We could have a mix of vessel sizes, which would make the optimisation much more interesting.
The brew plan

This is what we are trying to schedule, the brew plan. We just list the beer that we would like to produce here. A production plan will state exactly when each beer will be brewed, and then subsequently bottled. In the optimisation approach that I am presenting here, the order of the brew plan has some importance. It places a priority on the beers, so that the beers listed first should be earlier in the production plan.
An interesting aspect here is that the brew plan has the IPA and Pale Ale batches listed first. Then the Lager and Pilsner batches listed later. We will see that because we want to efficiently use the brewery equipment, some Pilsner and Lager batches are brewed before IPA and Pale Ale batches that are listed earlier.
Developing the production plan by hand
At this point, I would ask whether you think it is possible to produce a production plan by hand?
The short answer is yes. However, it depends on how much time you want to spend on developing the production plan. I would expect that developing a usable production plan for this example will take a 10-15 minutes of concentrated effort. For larger breweries, you could be looking at hours to days.
It is possible to use some simple rules, such as first-listed-first-brewed, which could make the process even quicker. But such plans will have a lot of inefficiencies in them. For example, the beers with the longest fermentation/conditioning time come later in the example brew plan. This means that the conditioning vessels will be sitting idle for much of the time. As a result a first-listed-first-brewed approach would produce a plan that takes 79 days to complete.
I encourage you to get out a spreadsheet to see whether you could do better than a 79 day brew cycle. There are some simple changes that will improve that result.
How can optimisation help?
At first, we need to think about what is our goal in developing the brew plan (beyond just brewing the beer). For example, you could have the goal to
- reduce the amount of time that fermentation vessels are empty,
- reduce the time it takes to complete all planned brews,
- or increase the profit from the brewed beer.
Each of these are called objectives, and they are what will be “optimised” when developing the brew plan. While the goals/objectives are very similar, the resulting brew plans can be quite different. For example, optimising to increase profit will lead to brew plan with the highest profit beers brewed first, and the lower profit beers brewed later. This could result in empty fermentation vessels, since there is a bottle neck in with the conditioning vessel.
Attempting to achieve these goals when developing a production plan by hand is very difficult. If you didn’t have any goal/objective, this would be described as a feasibility problem, in which all possible production plan are equally good. Adding in an objective is a way to score the production plans. Determining this score while developing the plan can be a challenging task.
The optimised production plan
In this example, I have used the objective to reduce the time it takes to complete all planned brews. This results in a compressed production plan. The outcome from the optimisation is


The first thing to note is that the Pilsners are brewed first. This may not be ideal from a sales point of view, but for the optimisation this helps in reducing the total brewing time since the conditioning vessels are put to use earlier. It would be possible to reoptimise this schedule with a few tweaks to get a “better-looking” schedule. That will be a topic of a later blog.
The second thing is that you can see some more idle time in the fermentation vessels early in the schedule, compared to later. This is again due to the choice of goal. If we wanted to reduce the amount of idle time, then we would get a different schedule that is more front heavy. An important thing here is that it shows it would be possible to brew more beers in a similar total brew time.
Finally, the total brew time for this schedule is 51 days. This is significantly less than the simple first-listed-first-brewed approach. This means that with a different schedule, you could fit in many more beers, thus increasing sales.
As a post script to this section, the time it takes to produce the schedule using optimisation software is around 30 seconds. This is in contrast to the 5 minutes it takes to produce the first-listed-first-brewed schedule. If you were to try and find an efficient schedule by hand, it could take much longer.
Should you choose optimisation?
It really depends on how big your brewery is and what you are trying to achieve. If you are running a very small brewery, even at the size of the example, optimisation will bring only a small improvement to producing a schedule by hand. If you have a brewery that is at least twice the size of the example, then that is where optimisation software can really help. As the brewery size increases, the complexity of the production planning grows exponentially.
If you want to get the most out of your brewing equipment, then try out optimisation. It could even just be as a proof of concept to see whether you can improve your production planning. It is possible that you are a gun at developing production plans. If that is not you, I recommend experimenting with optimisation software to see if it can help improve your brewery.